Maximum safety in potentially explosive atmospheres
Relevance of ATEX for dedusting
Dust explosions can have devastating consequences. Frequently, this can also result in the loss of human life. To protect people and employees in potentially explosive atmospheres, the European Union issued its ATEX directives.
Many organic materials, such as wood, sugar or grain – as well as numerous chemicals and light metals – can be combustible. When processed, they produce combustible dust as a by-product of milling, grinding or cutting. This dust has an extremely large surface area and can ignite at corresponding oxygen concentrations or form an explosive mixture. The lower its minimum ignition energy (MIE), the greater the danger.
Explosion protection is therefore an essential safety aspect in production facilities. Suitable protective measures, such as the selection of the right filter elements, are designed to minimize risk.
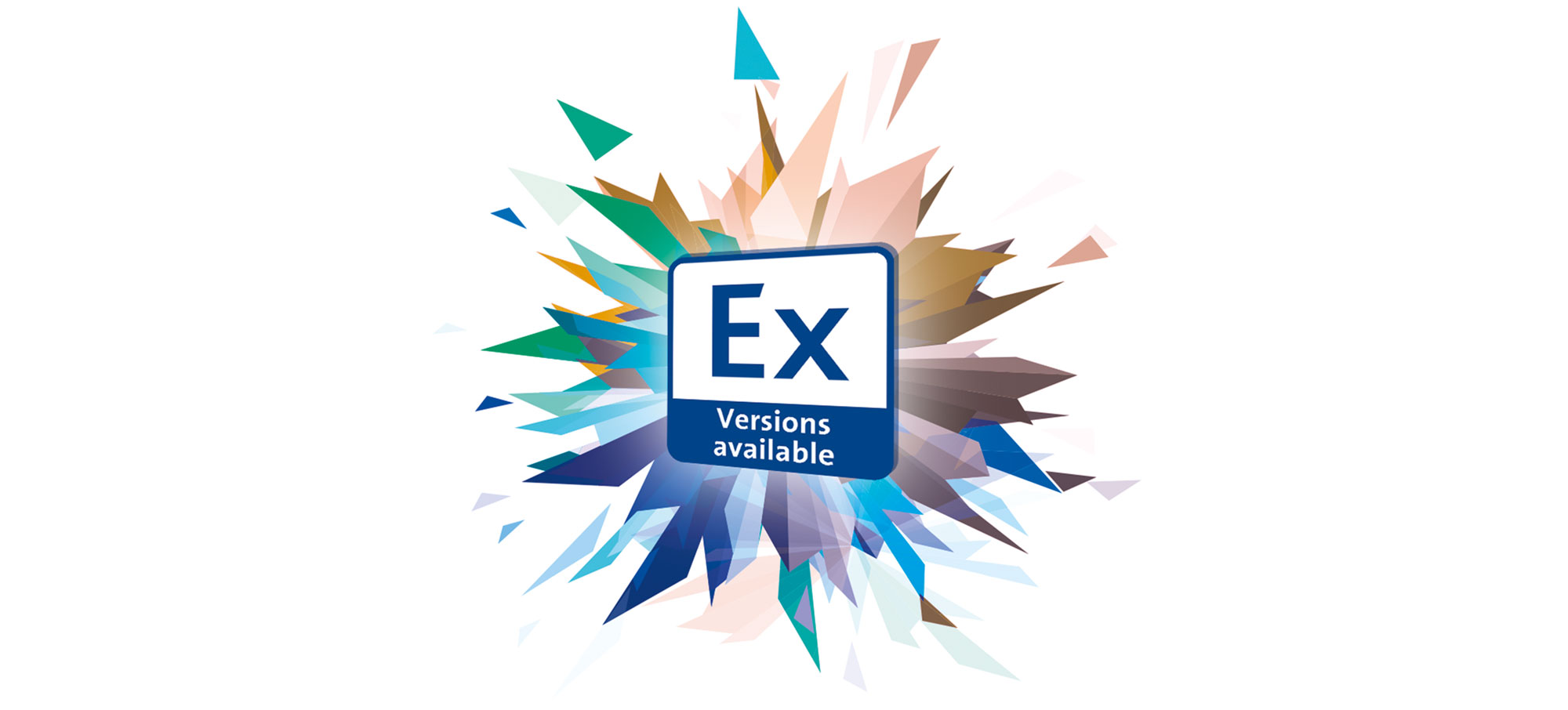
The two ATEX directives in brief
The designation “ATEX” is derived from the French abbreviation for ATmosphères EXplosibles. It currently comprises two directives: the ATEX Workplace Directive 1999/92/EC and the ATEX Equipment Directive 2014/34/EU.
ATEX Workplace Directive 1999/92/EC
If a potentially explosive atmosphere is present, the plant operator must prepare an explosion protection document as part of a risk assessment. This document must classify areas with explosive atmospheres into ATEX zones.
When selecting cleanable filter cartridges (LP), however, it is not relevant which ATEX zone the plant operator has defined. It is only necessary for the operator to know whether there is an ATEX zone in the dedusting system.
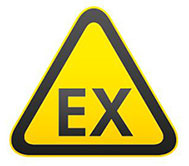
An explosive dust atmosphere is ... | … constantly, over long periods of time or frequently present. | … occasionally present during normal operation. | … not usually present during normal operation or only for a short time. |
Zone | Zone 20 | Zone 21 | Zone 22 |
ATEX Equipment Directive 2014/34/EU
The ATEX Equipment Directive specifies which equipment, components and protective systems may be used in explosion-endangered areas (ATEX zones).
Filter elements are not devices in the sense of the ATEX product directive and therefore do not require a CE designation. However, the requirement for compliance with practical explosion protection or conformity with the basic safety requirements remains. For this reason, we subject every conductive filter element to an individual test with regard to its conductivity. This is certified by our manufacturer attestation.
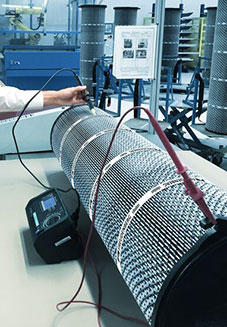
Single item testing of ATEX products
Our ATEX products for dedusting applications have to be tested for their suitability. A corresponding certificate must be enclosed with each tested ATEX product.
We ensure the suitability of our conductive filter cartridges (LP) by testing them individually. With the subsequently issued certificate, we confirm to our customers that the tested filter element falls below the limit value for conductivity.
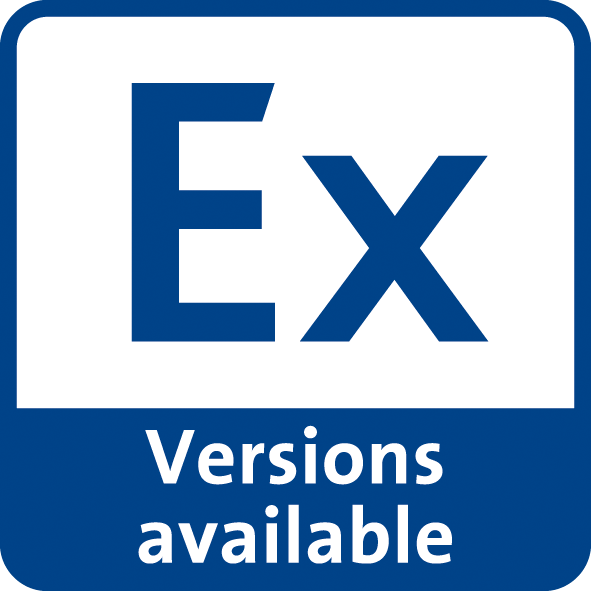
The right filter elements for your ATEX zone
To be able to support you in equipping your dedusting plant with the right filter elements, we need you to provide just two pieces of information:
- Is your dedusting plant an ATEX zone?
You only have to be able to answer this question “Yes” or “No”, since the zone classification has no relevance for the selection of the filter cartridges (LP). - Which dust explosion group does your dedusting plant belong to?
The filter element you can use in your system depends on the dust explosion group. For example, not all ATEX products are suitable for conductive dusts.
We will be happy to assist you in selecting the right filter elements for your dedusting plant.
ATEX Wiki
-
Discharge capacity
ATEX distinguishes between conductive, dissipative and insulating materials and objects. The boundary between dissipative and insulating varies depending on the application and object.
According to TRGS 727 (avoidance of ignition hazards due to electrostatic charges), filter nonwovens are subdivided according to their electrical strip resistance as follows:
Insulating: R > 10^8 Ohm
Discharging: R < 10^8 Ohm
Conductive: R < 10^4 OhmAccording to TRGS 727 and ISO 60079-32-1, the discharge resistance of a discharging filter must not exceed 10^8 Ohm.
-
Equipment
According to ATEX 2014/34/EU, equipment is defined as machines, apparatus, stationary or mobile devices, control and equipment components, as well as warning and prevention systems that are intended, individually or in combination, for the generation, transmission, storage, measurement, regulation and conversion of energy and/or for the processing of materials, and which have their own potential ignition sources and can therefore cause an explosion. Example: Freudenberg PulseWatch.
-
Equipment and explosion groups
Equipment groups according to ATEX 2014/34/EU
ATEX 2014/34/EU distinguishes between the following equipment groups:
- I Mining (underground / above ground)
- II Other applications (not mining)
Explosion groups according to TRGS 727
TRGS 727 (avoidance of ignition hazards due to electrostatic charges) distinguishes between the following explosion groups:
- I Mining (underground / above ground)
- II Gas explosion groups
- III Dust explosion groups
The dust explosion group III is subdivided again according to the type of dust:- IIIA combustible flyings
- IIIB Non-conductive dusts
- IIIC Conductive dusts
-
Manufacturer attestation
For your safety, we issue a written manufacturer attestation for our filter cartridges (LP). In this certificate, we certify that the filter element meets the essential health and safety requirements for its intended use in explosion-endangered areas.
-
Declaration of conformity for equipment
In the case of equipment (assemblies), the manufacturer is obliged to under run a conformity assessment procedure by a notified body of the EU and declare conformity of each product. The declaration of conformity contains both the ignition hazards of the individual parts and the ignition hazards resulting from their combination (assembly). It certifies that the device complies with the essential health and safety requirements for intended use in explosion-endangered areas.
-
Minimum ignition energy (MIE) of dusts
Among other things, minimum ignition energy assesses the combustibility of swirled dust in an explosive atmosphere and is an important parameter for the design of a plant. It describes the lowest level of energy that is sufficient to ignite an explosive fuel-air mixture during a discharge.
If the MIE is < 3 mJ (mJ = millijoules), discharging filter elements are specified. Regardless of the MIE, conductive filter materials are always required for dusts of explosion group IIIC (TRGS 727). -
Protection Systems
According to ATEX 2014/34/EU, protection systems are defined as all installations, with the exception of the components of the equipment defined above, which are intended to stop impending explosions immediately and/or limit the area affected by an explosion and are separately placed on the market as autonomous systems.
-
TRGS 727 – Avoidance of ignition hazards due to electrostatic charges
The TRGS 727 (TRGS = “Technische Regeln für Gefahrstoffe” or “technical rules for hazardous substances”) deals with the avoidance of ignition hazards due to electrostatic charges in explosion-endangered areas. It assists in evaluating the hazards and regulates the procedure for selecting and implementing protective measures to avoid these hazards.
Benefit from our specialized expertise about ATEX.
Select and request detailed information.
Discover our products for air pollution control.
Click details for more information. Technical data and specific product features can be found in the e-catalogue.
Ideal for simple upgrading of typical systems. Long lifespan even under extreme operating conditions. Especially effective in the separation of abrasive or chemically aggressive dusts. The service life can be extended by washing.
Special design details and the availability in all geometries customarily demanded by the market ensure efficient dust removal. Equipped with 3- or 4-hook injection molded flange, spacer ribs on both sides and centering collar.
Tool-free, easy installation on the clean air side, with no laborious screwing work. Simply press firmly and the patented snap hooks lock into place. Perfectly suited for use in suction excavators and cleaning vehicles.
Equipped with corrugated polyester filter medium and nanofiber layer. For the protection of people and machines, they achieve optimum values when dealing with fine dust and smoke. This extends the service life and improves energy balance for the system's operator.
With original Evolon® technology. Outstanding advantages over needled felt bags. 50% lighter, simple handling for cleaning and installation. For sustainably low emissions and reduced energy costs.
Master difficult dust removal tasks while complying with statutory residual dust emission values. Compact, space-saving design with pleated filter media. Regenerated via typical cleaning and washing.
Many different variants: Media with sinusoidal corrugation and patented pleat stabilization, with corrugation plus nanofiber layer or with antistatic features for high operational dependability in contact with explosive dusts.
PulseWatch
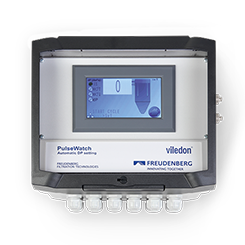
Freudenberg PulseWatch is an individually configurable device for the intelligent control and automation of compressed air cleaning in a dust removal system.