The service program for the pharma industry
Customized service packages for hygienic air quality
Hygienically clean air controls the quality of process air that comes into contact with pharmaceutical products and maintains a safe working environment. Optimize your processes and benefit from the economically efficient and energy-efficient solutions provided by our Viledon FilterCair service modules.
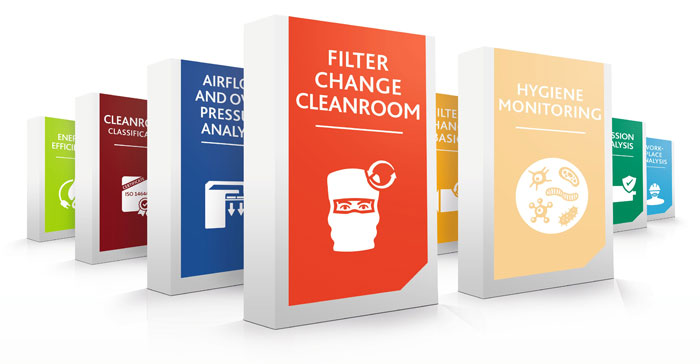
Is your air filtration system not working properly?
Together with you we will analyse your process conditions and find a solution.
With its numerous modules, Viledon FilterCair provides answers to your questions about air filtration systems for cleanrooms and the pharmaceutical industry. We have summarized the most important for you.
-
How can I ensure stable, hygienic air quality in my ventilation system?
The first step can be to carry out a comprehensive review of the current state of your ventilation system and its specific components, from air inlet to air outlet.
After implementation of the measures proposed by us, we carry out a repeat inspection to check the intended achievement of objectives. As a further step, the focus is on determining the total germ count; this mainly comprises microorganisms. With regular hygiene inspections and the collection of airborne germs according to VDI 6022:2018, the risk of contamination can be reduced to a minimum.
We will be pleased to check your plant according to VDI 6022:2018 and carry out an initial or repeat hygiene inspection, including airborne germ measurements. All inspections can be carried out as part of an individual Viledon FilterCair service contract. We will happily provide you with further advice. -
How can I achieve audit reliability for my ventilation systems?
All our regular inspections or complete service and maintenance programs for ventilation systems and cleanrooms are accompanied by meaningful and audit-compliant reports. The individual inspections and analyses can form part of a Viledon FilterCair service contract and are individually adapted to the requirements of your system concept.
-
How can I ensure that my ventilation systems continue to operate smoothly, despite a shortage of personnel or time?
With our Viledon FilterCair air quality management service, we are the ideal partner. Our experienced service technicians are either masters or technicians trained to VDI 6022 Category A. All the work required in connection with your ventilation system is carried out professionally and efficiently by our experts. As well as hygiene inspections, special measurements and tests, we also organize filter changes including the delivery of high-quality Freudenberg filters. Simply get in touch and we will work with you to create a suitable concept for your needs.
-
I keep finding fibers behind a filter stage – why is that?
Some glass fiber media can break during the start-up and shut-down process of your plant and thus release glass fibers into the air. These then settle in the subsequent registers or enter the spaces to be ventilated via the ventilation ducts, if no additional filter stage is installed. This cannot happen with filter media made from synthetic fibers – the nature of the material itself prevents this. We will be pleased to advise you on the correct choice of filter.
-
What are the right air filters and filter classes for my ventilation system? What do I need to be aware of?
Various standards and guidelines regulate the filter classes for different ventilation system applications.
For example, ISO 16890 regulates the required filter classification and quality.
VDI 6022 stipulates requirements for air conditioning systems in planning, production, execution, operation and maintenance that ensure hygienic operation for the protection of people. This includes, for example, the use of microbiologically inactive filters, and that the filter pockets have a high inherent rigidity and are suitable for operation at up to 100% humidity. The filter classes that need to be used are also clearly defined.
In contrast, DIN 1946-4 regulates the operation of air conditioning systems in buildings and rooms in the healthcare sector. It also describes the inspection of HEPA filters.
EN 13779:2007 regulates the ventilation of non-residential buildings and contains general principles and requirements for ventilation and air conditioning systems and room cooling systems.
There are various aspects to consider when choosing the right filters. We will be pleased to assist you with advice and support.
-
How can I reduce the energy consumption of my ventilation system?
Differently high pressure drops influence the energy consumption of the fan. Energy consumption can be significantly reduced by using energy-efficient air filters.
We can perform an energy analysis within the framework of a plant inspection. This involves checking individual components for their functionality. By means of an energy monitoring process, the current energy consumption can be precisely determined. In the course of a more detailed inspection, our experts inspect the complete ventilation system from a cooling capacity >12 kW according to § 12 of the German Energy Saving Ordinance (EnEV).
Using these values as a basis, we then draw up individual recommendations and optimization proposals aimed at reducing energy consumption effectively and in the long term. -
What do I need to be aware of when changing HEPA filters (from filter class H13 upwards)?
For HEPA filters from filter class H 13 upwards, a performance measurement must be carried out by the filter manufacturer in accordance with EN 1822:2012. This involves passing defined aerosols through the filter. Particle counters measure their number before and after the filter and thus determine the actual separation efficiency.
Where HEPA filters are changed in a cleanroom, they must be checked by our trained Viledon FilterCair service personnel for possible leaks and to confirm that they fit tightly, among other things. These checks form part of the cleanroom approvals process according to EN ISO 14644.
-
How can I have my cleanrooms certified to EN ISO 14644?
Cleanrooms and associated cleanroom areas must be certified according to EN ISO 14644 before they are put into operation. Among other things, the standard regulates the respective specified degrees of air purity. Rooms are classified according to the number of particles per cubic meter of air. This ensures that the room complies with all clean air criteria.
Using a variety of measurements, we determine the ISO class of cleanrooms according to EN ISO 14644. When establishing the air exchange rate, it is necessary to ensure that the entire room volume is recorded and exchanged. Furthermore, we also determine the recovery time of the cleanroom, i.e. how long it takes for the cleanroom to clean itself in the event of increased local contamination. Depending on its area of application, a cleanroom is operated at either overpressure or underpressure. This must always be kept constant and permanently controlled.
We would be pleased to support you in the inspection and certification of your cleanrooms according to EN ISO 14644.
Regular hygiene inspections and individual on-site service
Benefit from our all-in-one Viledon FilterCair air quality management package
Choosing Viledon FilterCair also ensures that you guard against inadequate maintenance of air handling units (AHUs) and the filter systems they contain. Malfunctioning or heavily soiled filters support bacterial growth and allow all sorts of contaminants to enter production areas, from pests to fungal spores and microorganisms.
Our Viledon FilterCair experts regularly carry out on-site inspections and measurements to ensure a hygienic production environment. This results in high-performance, economical and environmentally friendly management of air quality
In addition to the modules themselves, Viledon FilterCair also offers individual service contracts to ensure comprehensive air quality management. This includes the provision of all required filters plus customized services.
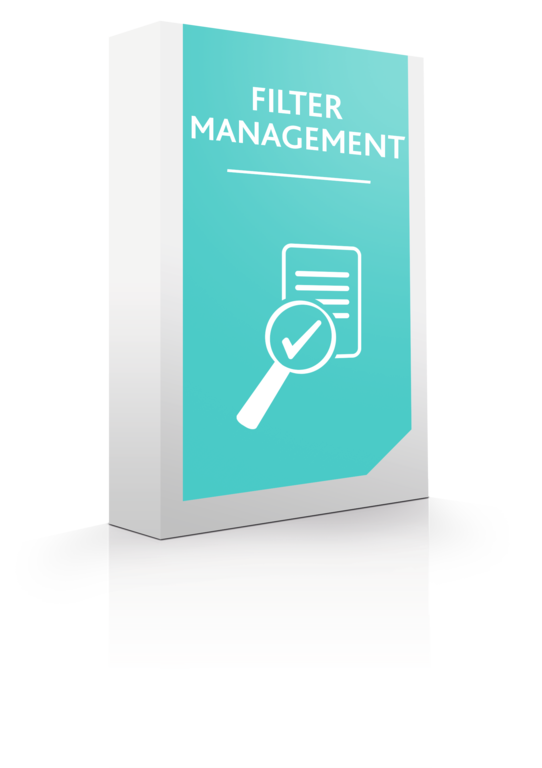
Viledon FilterCair service modules
Tailor-made service packages
With our modular Viledon FilterCair solutions, we offer you a comprehensive selection of application-specific services that can also be individually combined with each other.
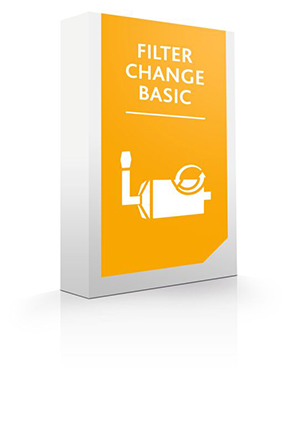
Module FILTER CHANGE BASIC
Scope of services:
- Planning and organization of filter changes
- Supply of high-quality filter elements for ventilation units
- Thorough cleaning of the filter chamber
- Professional replacement of panel filters, pocket and cassette filters
- Visual assessment of the system components, e. g. inspection of fans, cooling and heating register, drive belts
- Disposal of used filter elements (optional)
- Acceptance report
- Supply of additional high-quality filters as required, such as dust removal cartridges and filter bags
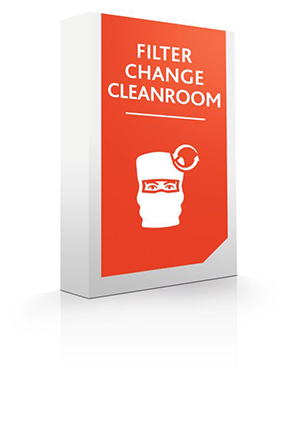
Module FILTER CHANGE CLEANROOM
Scope of services:
- Supply of high-quality HEPA / ULPA filter elements for high hygiene zones and cleanrooms
- Cleaning of the mounting frames
- Professional replacement of HEPA / ULPA filters
- Disposal of used filter elements (optional)
- Leak / impermeability test
- Integrity test
- Airflow determination
- Comprehensive documentation
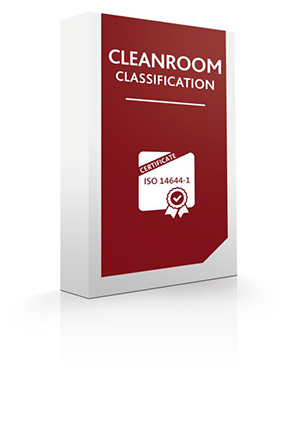
Module CLEANROOM CLASSIFICATION
Scope of services:
- Cleanroom inspection according to ISO 14644-1 or GMP
- Documentation and certification
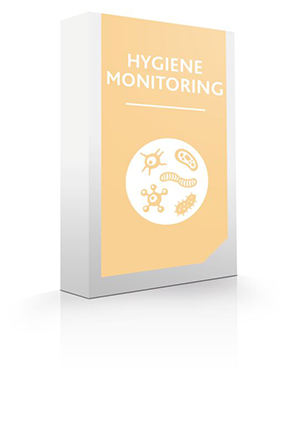
Module HYGIENE MONITORING
Scope of services:
- Determination of complete germ counts or complete colony counts in the air, on surfaces and in liquids (bacteria, fungal spores,
viruses …) - Swab test for final control of effective cleaning in critical plants
- Conclusive documentation on the present plant status
- Tests performed to German standard VDI 6022: Hygiene requirements for ventilation and air-conditioning systems and units
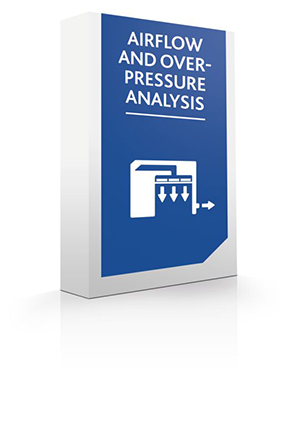
Module AIRFLOW AND OVERPRESSURE ANALYSIS
Scope of services:
- Visualization of the flow conditions at production or workplaces
- Detailed video analysis of the airflow conditions
- Checking velocity of airflow and measurement of overpressure
- Temperature and relative humidity measurements
- Checking the ventilation unit (filter audit)
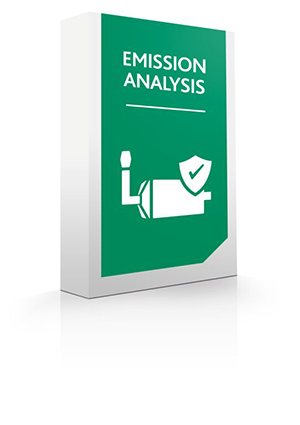
Module EMISSION ANALYSIS
Scope of services:
- Emission value measurement of the exhaust air concentration
- Verification of compliance with emission limit values in accordance with country standard
- Determination of dust mass concentration acc. to EN 13284 (European Standard)
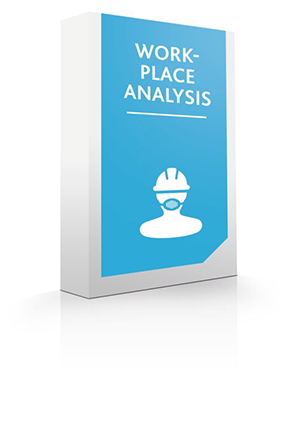
Module WORKPLACE ANALYSIS
Scope of services:
- Review of occupational safety limit values
- Measurement of the maximum workplace concentration
- and statement on PM values
- Determination of air quality
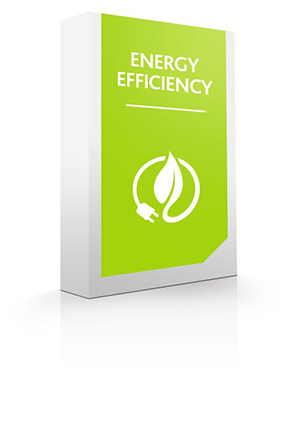
Module ENERGY EFFICIENCY
Scope of services:
- Ventilation consultancy including air volume balances
- Energy efficiency consultancy for air handling units
- Equipment inspection according to § 12 EnEV
Benefit from our expertise in the pharma industry.
Select and request detailed information.
Discover our products for cleanrooms and pharma.
Click on details for more information. Technical data and specific product features can be found in the e-catalog.
Robust in sustained use, high operational dependability and reliability even in the face of extreme moisture and wet conditions. They enable the energy-efficient operation of air conditioning systems. This translates to energy cost savings and a reduction in CO2 emissions.
The premium class in patented quality. Highly stable filter designs for the greatest possible operational dependability even under extreme loads. Water-repellent. Long service life, making them very economical.
Optimal price-performance ratio in the operation of ventilation systems plus simple and safe handling. MVP 95 filters achieve energy efficiency class A. Energy cost savings and reduced CO2 output.
Robust and extremely dependable in hygienic quality. With water-repelling hybrid synthetic nonwoven media (HSN) suitable for use in damp environments. Ideal for air-conditioning systems.
Satisfies the highest clean air and sterility requirements. Flow-optimized geometry and equidistant folds thanks to MiniPleat technology. Especially economical and reliable operation.
For mounting systems with sword profile. The MiniPleat technology ensures a homogeneous media velocity for economical operation. Moisture-resistant and microbiologically inactive.
Reliable operation thanks to high-arrestance micro-glass fiber papers and a flow-optimized geometry. The stable design is moisture-resistant and microbiologically inactive.