Looking inside the microcosm of car painting
With the Viledon FilterCair module “Basic + Dirt in Paint”, Freudenberg brings the cause of the tiniest paint defects into the light of day.
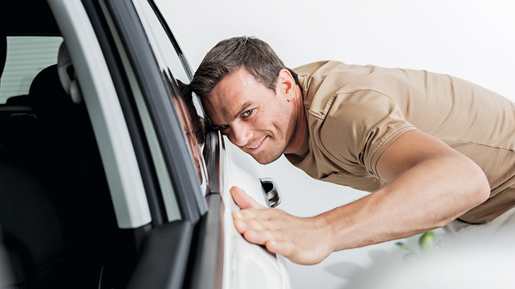
But what is the source of these ever recurring faults in the coating of plastic parts? A wetting defect?
The experts at Freudenberg Filtration Technologies should be able to assist in solving and clarifying this question. Under the name Viledon FilterCair, the company combines its flexible, individually tailored complete service package, aimed at the qualitative and economic optimization of coating processes. For many years, Viledon FilterCairhas symbolized the holistic understanding of the filtration experts at Freudenberg: offering customers not just filters, but consistently high air quality; acting not only as product suppliers but as consultants and problem-solvers too. Since 2017, Freudenberg Filtration Technologies has also been providing this expertise on a demand-driven basis outside fixed service contracts, including for the BMW Group’s Landshut plant.
First step:
Status analysis of the painting zone
Back to the specific case at BMW. As the BMW Group already relies on Viledon® filters for the purity of its painting processes at its plant in Lower Bavaria, the two Viledon® Site Engineers, Pascal Brodhun and Stephan Wassermann, were already familiar with the local situation. A status analysis of the paint zone is usually the first step in seeking to identify the cause, since the causes can be as diverse as the paint defects themselves. Potential sources include fiber or dirt inclusions, paint overspray, pollen, wetting defects caused by application technology, contaminated compressed air, silicone-containing lubricants and oils, dirt carried in by employees as well as on their clothes or tools. “Due to the large number of possible sources of contamination, it is necessary to look at the process holistically and to examine it onsite. No two cases are alike”, explained Christian Westenburger, Contract Manager Viledon FilterCair.
A thorough filter analysis and evaluation, meaningful particle, temperature, humidity and volume flow measurements and determining the sinking speed in the paint line - these are the key components of the Viledon FilterCair module “Basic”. However, they did not reveal anything unusual at the BMW Group plant in Landshut. The painting process was flawless: the work processes were stable, all systems were set up correctly and the air balance in the spray booth was perfectly in order.
“Our aim is to systematically rule out possible sources of error step by step”, commented Michael Steuer, Regional Manager Viledon FilterCair, describing the procedure. “One element of this is the process or root cause analysis on site. At the same time, we began detailed paint damage analysis for BMW in our laboratories”, he explained. This second approach with the Viledon® Viledon FilterCair module “Basic + Dirt in Paint” was the successful one in this specific case.
Second step:
Problem-specific analysis under high performance microscopes
During this process, Freudenberg experts immerse themselves in the microcosm of the plastic paint. To begin with, they use incident light microscopy. “This showed us an inhomogeneous surface. In some places, there was no basecoat at all. At the same time, however, since the entire defect was covered with clear lacquer, we were able to exclude a wetting defect caused by silicone or similar”, explained Michael Steuer.
The problem thus had to lie deeper, in the true sense of the word. This brought an electron microscopic (SEM/EDX) analysis into play. In this case, the faulty spot is precisely cross-sectioned and inspected in cross-section to find out which elements are causing the flaw. What may look to the layman like a variety of differently colored images set the Freudenberg experts immediately on the right track.
Any color that exhibits the circular to oval inclusions below the defect represents a chemical element that makes up this particle. In this specific case, that meant silicon and oxygen in particular, but also phosphorus, aluminum and a little potassium.
Freudenberg then examined the granulate from which the car catchers were sprayed. “From samples, we produced wafer-thin films with a melting temperature of 280°C”, explained Frank Hofmann, Contract Manager Viledon FilterCair. This granulate analysis showed that the quartz particles found were a constituent of the raw material. In places where they were too coarsely grained, painting errors emerged. Problem solved. This fulfilled the most important goal: a satisfied customer.